How Does Sand Casting Compare to Other Casting Methods?
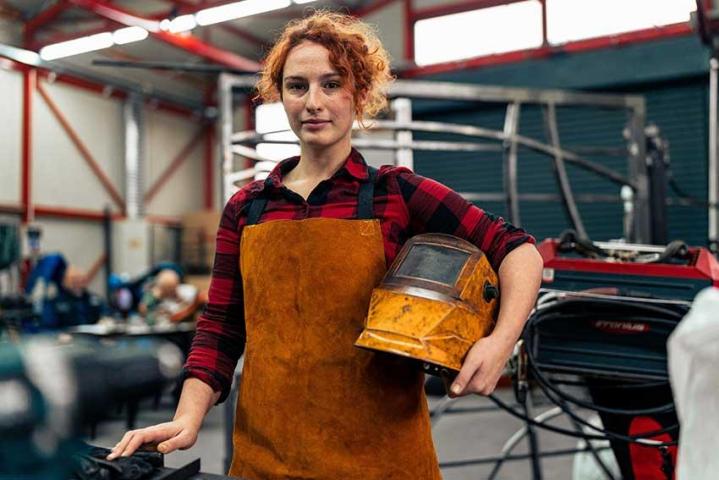
Sand casting is one of many casting methods available, each with unique benefits and limitations. Comparing these methods helps determine the best approach for different applications.
Sand Casting vs. Die Casting
Sand casting is known for its versatility and ability to produce large, complex parts at a relatively low cost. It uses expendable sand moulds, making it ideal for lower production volumes or projects that require flexibility in design. In contrast, die casting utilises permanent metal moulds, which allows for high precision and a superior surface finish. Die casting is more cost-effective for large-scale production runs but has higher initial tooling costs.
At Alliance Connect, we help clients choose between sand casting and die casting based on their specific needs, considering factors like production volume, budget, and desired component characteristics.
Sand Casting vs. Investment Casting
Investment casting, also known as lost-wax casting, offers exceptional detail and accuracy, making it suitable for intricate designs and thin-walled components. Unlike sand casting, which uses a sand-based mould, investment casting involves creating a wax pattern that is coated with a ceramic shell. While this method provides high precision and a smooth surface finish, it is generally more expensive and less suited for large parts.
Sand casting, with its ability to handle larger components and lower costs, is often preferred for applications where the fine detail of investment casting is not required. At Alliance Connect, we guide clients through these options to find the most suitable casting method for their projects, ensuring optimal quality and cost-efficiency.