How Does Temperature Affect the Metal Casting Process?
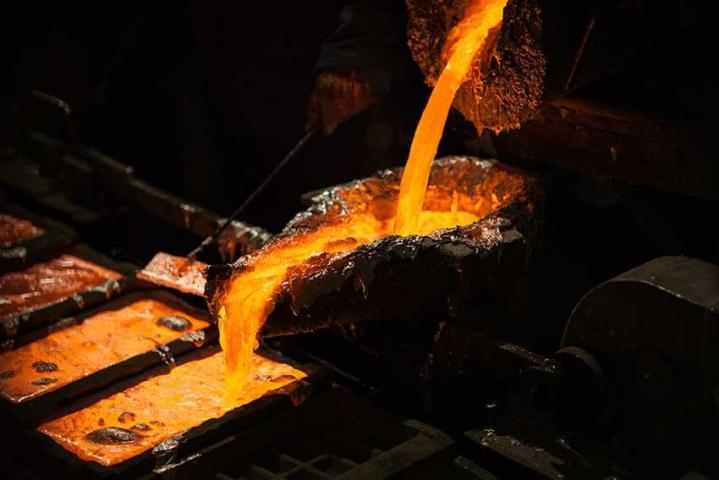
Temperature plays a crucial role in the metal casting process, influencing the quality and characteristics of the final product. Understanding its impact helps optimise casting outcomes.
Impact on Metal Flow and Solidification
The temperature of molten metal directly affects its flow characteristics and solidification process. If the metal is too hot, it can lead to excessive fluidity, which may cause defects such as turbulence or misruns. Conversely, if the metal is too cool, it might not fill the mould completely, resulting in incomplete castings or cold shuts.
Maintaining the correct pouring temperature ensures that the metal flows smoothly into the mould and solidifies evenly, reducing the risk of defects. At Alliance Connect, we carefully monitor and control the temperature of the molten metal to ensure optimal flow and solidification, achieving high-quality results for every casting.
Effects on Material Properties and Defects
Temperature variations can also influence the material properties of the cast product, including its strength, hardness, and overall integrity. High temperatures can improve fluidity and reduce defects, but they might also lead to increased oxidation and scaling. On the other hand, lower temperatures can cause brittleness or uneven material properties. Proper temperature control is essential to balance these factors and achieve the desired material characteristics.
At Alliance Connect, we employ advanced temperature management techniques to fine-tune the casting process, ensuring that each product meets the precise specifications and quality standards required by our clients.