What Are the Common Defects in Sand Casting and How Can They Be Prevented?
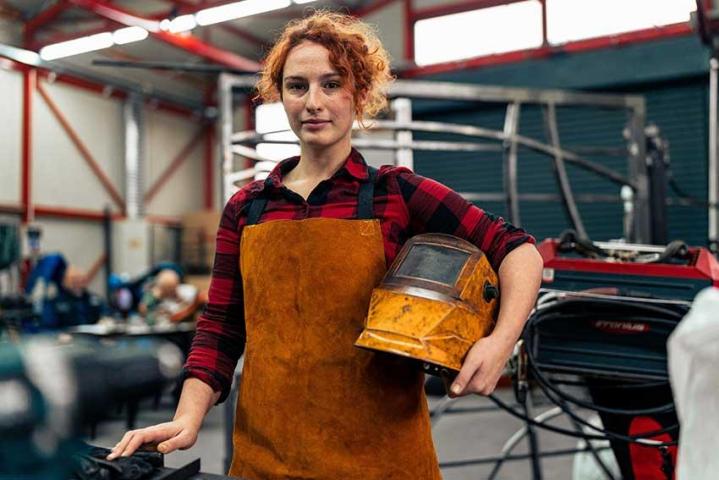
Sand casting can result in various defects that affect the quality of the final product. Understanding these defects and their causes helps in preventing them effectively.
Common Defects in Sand Casting
Some common defects in sand casting include porosity, misruns, and sand inclusions. Porosity occurs when gas is trapped within the molten metal, leading to small voids or cavities. Misruns happen when the molten metal solidifies before completely filling the mould, resulting in incomplete castings.
Sand inclusions occur when loose sand grains become embedded in the casting surface. These defects can compromise the strength, appearance, and functionality of the final product. At Alliance Connect, we carefully monitor the casting process to identify and address these defects early, ensuring high-quality castings.
Prevention Techniques
Preventing defects in sand casting involves several strategies. To reduce porosity, proper venting of the mould is essential to allow gases to escape. Ensuring the correct pouring temperature and speed can help prevent misruns by allowing the molten metal to flow smoothly and fill the mould completely. To avoid sand inclusions, the mould should be compacted correctly, and the sand quality must be maintained to prevent loose grains.
At Alliance Connect, we implement stringent quality control measures throughout the casting process, from mould preparation to final inspection, to minimise defects and deliver reliable, high-quality castings to our clients.