What Are the Most Common Defects in Metal Casting and How Can They Be Prevented?
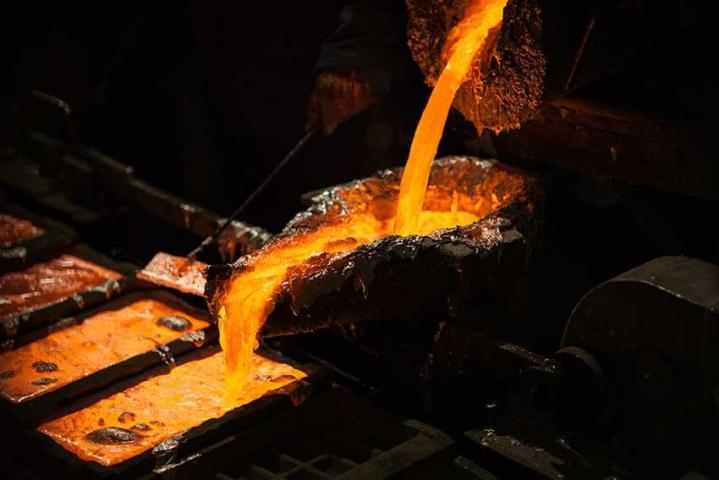
Metal casting, while versatile, can be prone to defects that impact the quality of the final product. Identifying these issues and knowing how to prevent them is crucial for achieving optimal results.
Common Defects in Metal Casting
Some common defects in metal casting include porosity, which are small holes or voids within the metal that weaken the structure, and shrinkage cavities, which occur when the metal solidifies and contracts. Another issue is inclusions, where foreign materials are trapped in the metal, compromising its integrity.
At Alliance Connect, we address these challenges by using high-quality materials and precise casting techniques to minimise the risk of defects. Our team conducts thorough inspections throughout the casting process to ensure that any potential issues are identified and rectified promptly.
Preventing Casting Defects
Preventing casting defects involves careful attention to several factors, including the design of the mould, the quality of the metal, and the casting environment. Ensuring that the mould is properly vented can help reduce the risk of gas-related defects, while controlling the temperature of the molten metal can prevent issues like shrinkage.
At Alliance Connect, we implement stringent quality control measures and utilise advanced casting technology to address these concerns. By optimising each stage of the casting process, we ensure that our products meet the highest standards of performance and durability, minimising defects and enhancing overall quality.